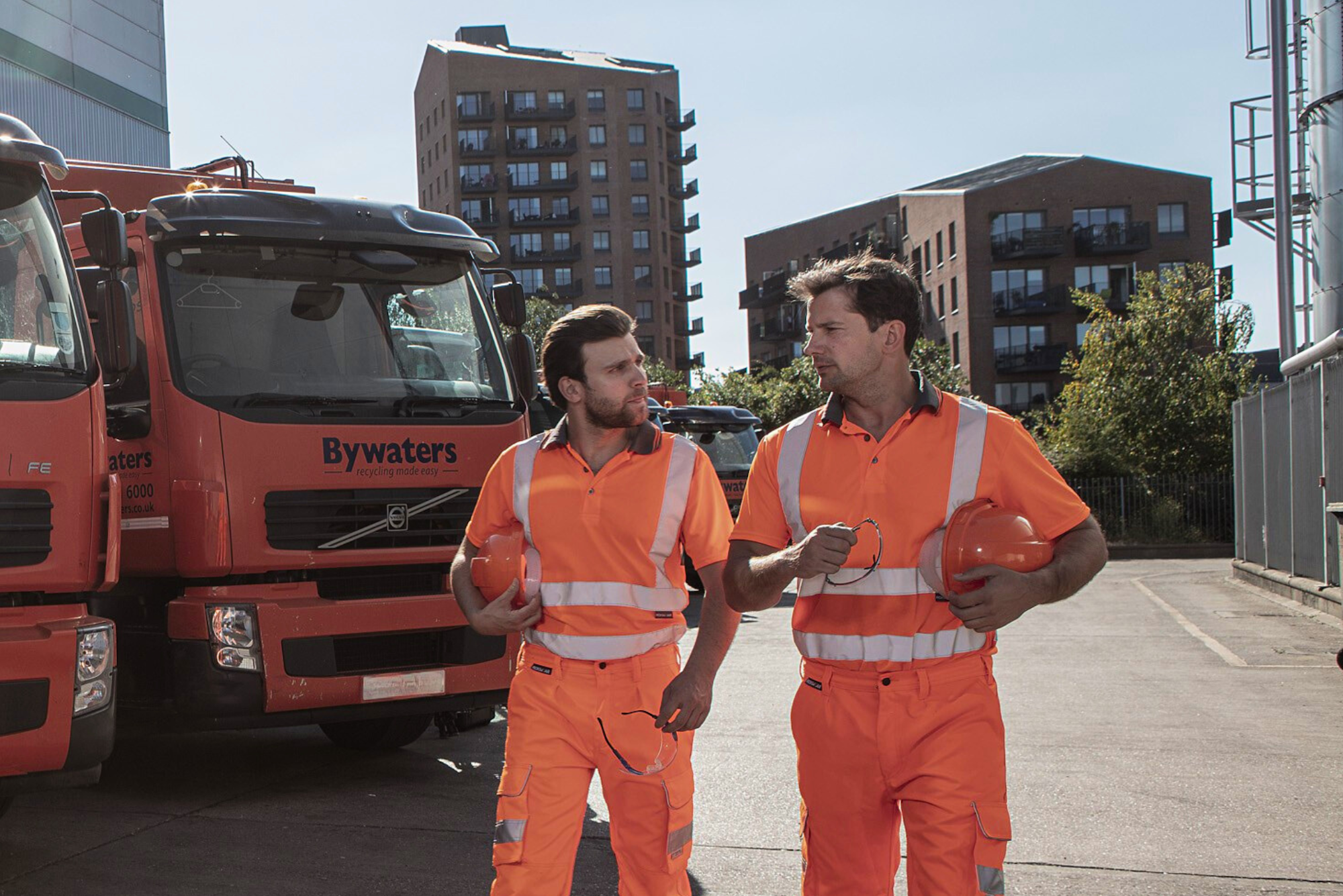
Featured
Your definitive guide to summer workwear
From summer workwear to breathable PPE - learn how to stay safe and cool on the job this summer.
The latest news and blogs from SMI.
Public Sector
Cut costs, save time, and keep teams safe with one trusted supplier for all your PPE and workwear needs.
Public Sector
Learn about hi-vis PPE laws, EN ISO 20471 standards, visibility classes, and compliance tips.
Public Sector
Discover the differences between water-resistant and waterproof PPE, and find the right workwear for your team.
Public Sector
Reduce workplace injuries by making sure your employees know how to use a safety knife. Stay safe and HSE compliant with our simple guide.
Public Sector
Want to know how powered respirators can make your workplace safer? From the benefits to what to look for, this guide has it all.
News & Blog
Learn all about the latest EN ISO 20345:2022 safety footwear standards, what's changed, and how to choose the right safety footwear for your team.